
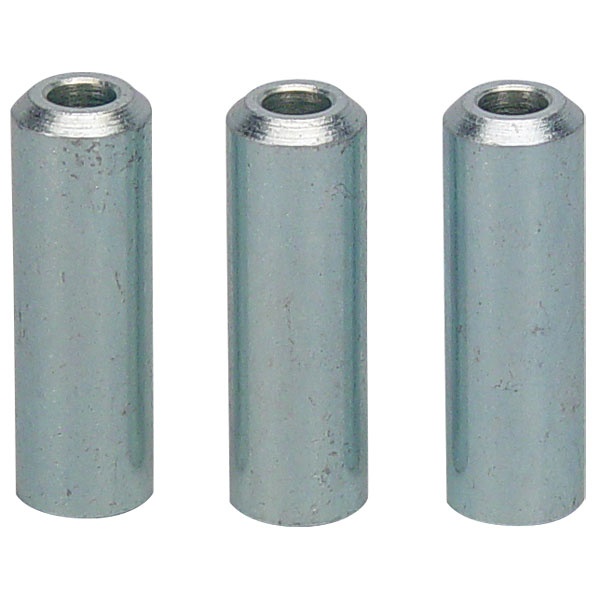
But how do you fix this? Upgrading the air compressor systemįor industrial blasting applications, you may need to add a multi-stage air drying system. If you are blasting continually, and the air compressor has no time to cool down, the condensation may cause jamming in the lines. The warm air from the supply line is usually the source of condensation. The blast cabinet is cooler than the air from the supply line because the dust collector blower is circulating air, cooling the inside of the cabinet. This pressurized air is then introduced to the blast cabinet, which is cooler than the air in the tank and compressor. Eventually, this warms the tank above room temperature. To understand why this happens, let’s look at the steps in the abrasive blasting process.Ĭompressed air is under pressure, so the air molecules become slightly warmer than room temperature, due to friction. If the air compressor does not have time to start, stop, and cool down during your blasting routine, it can cause excessive condensation. This is most commonly caused by having an air compressor that is slightly undersized for the blast cabinet volume. If you have too much moisture in your air or abrasive lines, this can cause abrasive flow issues. Removing unwanted moisture from hot, compressed air Excessive moisture in the air and abrasive lines can be the root cause of many problems with abrasive flow in sandblasters. This is one of the most important maintenance items for sandblasting cabinets. You should drain the water trap every time you use the compressor in blasting to prevent rust. If you live in an especially humid location, it may fill up even faster. The water trap fills up about once a week under regular use. If the water trap on the air compressor is full, that condensed liquid water can evaporate and re-enter the air line to the blast cabinet. The air typically exits through a filter, which removes other small particulates from the air. Air enters one side, and circulates around the recess, where condensed water from the air accumulates at the bottom of the trap. Water traps remove already condensed water in the air compressor line. If your blasting gun seems to be lacking the force it did in the past, it may be time to get a fresh blast nozzle.ĭrain the water trap (air filter) on your air compressor. The wider the nozzle orifice, the more air is needed to accelerate the media with the same force. The accelerated abrasive chews the nozzles up, widening the opening the compressed air and media is propelled through. The blast nozzle may be worn outīlast nozzles also wear out over time.
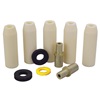
If your blast media is at this point, even if the intake hose picks it up, the blasting power will be ineffective. Every type of abrasive media has a certain number of uses before it fragments into particles too small to effectively strip and clean a surface. If the abrasive has passed its maximum number of recycles, it needs to be disposed of and the abrasive in the tank replenished.

Your abrasive media may be spentĪbrasive doesn’t last forever. If there is still plenty of abrasive in the tank, check the valves. You might need to add more abrasiveĪnother possibility if you have air flow, but no media, is that you need to add more abrasive to the tank. If there is air flow at the gun, but no abrasive is coming through, the abrasive pickup line is probably clogged. Usually, particles like burrs, paint chips, rust fragments, decals or other particles are clogging the line at either the gun or the other end of the pickup line. Remove the nozzle from the blast gun, inspecting the passageway for any obstructions. If your blast gun is not drawing any abrasive, turn off the compressed air supply. If there is an inadequate supply of air, the compressor may be faulty. Check the air compressor output pressure gauge to see if there is sufficient air pressure when the compressor runs. If your abrasive media flow seems off, check the air gun to see if the correct air pressure is being produced by the air compressor. This is a list of things to check if you have ruled out the most obvious problems. Today we are talking strictly about troubleshooting abrasive flow issues in siphon blast cabinets. Siphon blast cabinets differ from pressure blast cabinets, where the abrasive media and air are compressed in a pressure pot, then expelled through a single hose through the blast nozzle. Here, the compressed air and abrasive mix together, and are expelled through the blast nozzle. This type of blast cabinet has a line for compressed air, and a line that siphons abrasive media to the blasting gun. The most common type of dry blast cabinet is a siphon blast (aka suction blast) cabinet.
